June 15, 2007
Scientist's new process could mean cheaper fuel
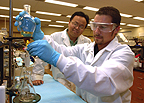
Caption follows story
CARBONDALE, Ill. — Restaurant owners look at the dark, smelly drippings in their grease traps as an overhead cost and liability. Who can blame them? They have to pay someone to haul the stuff away.
But a scientist at Southern Illinois University sees great opportunities in those grease traps.
Yong Gao, associate professor in the Department of Chemistry and Biochemistry in the College of Science at SIUC, believes he's found the chemical means to turn so-called brown grease and yellow grease — food industry terms for oils previously used to fry things — into biodiesel fuel to run automobiles. His process also will turn a low-grade byproduct of traditional biodiesel formulation — glycerin — into the valuable, high-grade type sought by the pharmaceutical industry.
Later this summer, Gao will open Midwest Energy Group Inc. at the SIUC Small Business Development Center. A small team will then run tests and do engineering design for full-scale production using the concept, which Gao says he has proven will work in the lab.
Midwest Energy is one of the latest ventures put together with the help of the University's Office of Research Development and Administration's technology transfer program. The program helps professors market their discoveries and file for patents while securing an interest for the University where appropriate.
Gao, who has filed for two patents related to his novel application of the chemical processes involved, also is negotiating with top chemical industry corporations. The companies have shown a serious interest in Gao's process, which eliminates the need to use very pure oils in the manufacture of biodiesel fuel while creating a marketable byproduct.
"We've been working only a short time and so far we have almost entirely confirmed our ideas in the lab," said Gao, who arrived at SIUC in 2000 after earning his doctorate in bio-organic chemistry at the University of Alberta, Canada, and doing post-doctoral work at Harvard University. "We're almost ready to commercialize this process."
Gao began working on his project last year after reading an old scientific paper dealing with polymers. Gao realized the paper held promise in another area — transesterfication — a key process involved in the production of biodiesel.
"When I read this paper, I realized I can do something with biodiesel using this," Gao said. "I had my students run a sort of quick and dirty test, and it worked. I knew we had something."
In traditional biodiesel manufacturing, workers mix some sort of high-grade, pure organic oil — soy, vegetable, palm, etc. — with methanol and a catalyst before heating them up in a reactor, which is like a big oven. In about 30 minutes, the mixture transforms into biodiesel and low-grade glycerin, each lying at different separated levels in the reactor.
Gao's approach uses low-grade oils, such as brown or yellow grease, which typically contain substantial amounts of fatty acids. Such impurities are problematic in traditional biodiesel processes, but Gao eliminates that problem by pretreating the oils in another reactor with a different catalyst that causes esterfication — a chemical reaction often involving combining alcohol and acid to form an ester — resulting in the creation of biodiesel fuel. When the now-purified oil goes through the second reactor, not only does it create additional biodiesel fuel but also the high-quality glycerin.
The new process could mean cheaper fuels, a more environmentally friendly process and new markets for both the waste oils and the glycerin, which typically sells for more than 50 cents per pound. The process also would be a boon to the food industry, where such materials are a financial liability.
"Pure soy oil can sell for $2 a gallon or so,' Gao said. "But restaurants have to actually pay someone to haul away brown grease. We have the technology to take advantage of that cheap fuel and help the environment at the same time."
Biodiesel is becoming more popular worldwide, with some of the biggest potential markets in Europe, where a much higher percentage of automobiles use diesel engines. Southeast Asia, where palm oil often is used to make biodiesel, also holds great promise, Gao said, as his process can be adjusted to accommodate any type of organic oil.
"These places are hungry for technology," he said.
Gao plans pilot production tests this summer and fall and hopes to ink a deal with industry leaders as well.
He envisions SIUC becoming home to a biodiesel production demonstration plant, producing up to 10 million gallons a year while also training future engineers in this environmentally friendly process, convincing skeptical customers and generating revenues that allow the plant to be self-sustaining.
"It would be wonderful if we had people from all over the world coming to Carbondale to see how this works," he said.
Caption:
French-fried energy – Yong Gao, left, associate professor of chemistry and biochemistry at Southern Illinois University Carbondale, looks on as Philip D. Stevens, a senior in environmental chemistry from West Salem and the son of Don and Ruth Stevens, runs a test on a biodiesel fuel manufacturing processes. Gao believes he’s found the chemical means to turn so-called brown grease and yellow grease — food industry terms for oils previously used to fry things — into biodiesel fuel. His process also will turn a low-grade byproduct of traditional biodiesel formulation — glycerin — into the valuable, high-grade type sought by the pharmaceutical industry. Gao plans to open Midwest Energy Group Inc. at the SIUC Small Business Development Center. A small team will then run tests and do engineering design for full-scale production using the concept, which Gao says he has proven will work in the lab.
Photo by Steve Buhman